Custom box inserts are tailored to the precise size of your products, keeping them secure in transit while giving your customers a truly elevated unboxing experience.
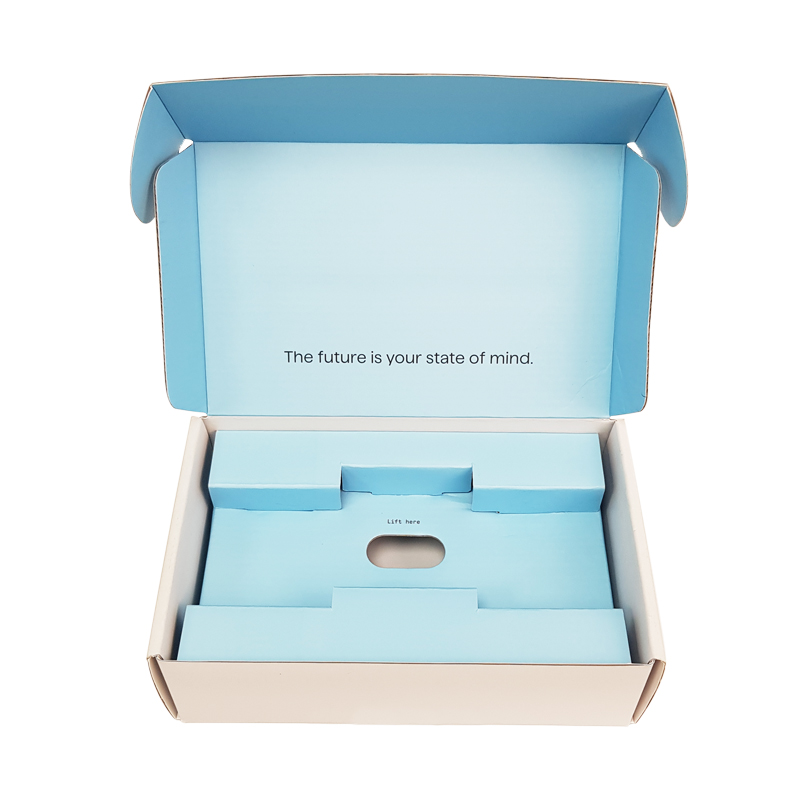
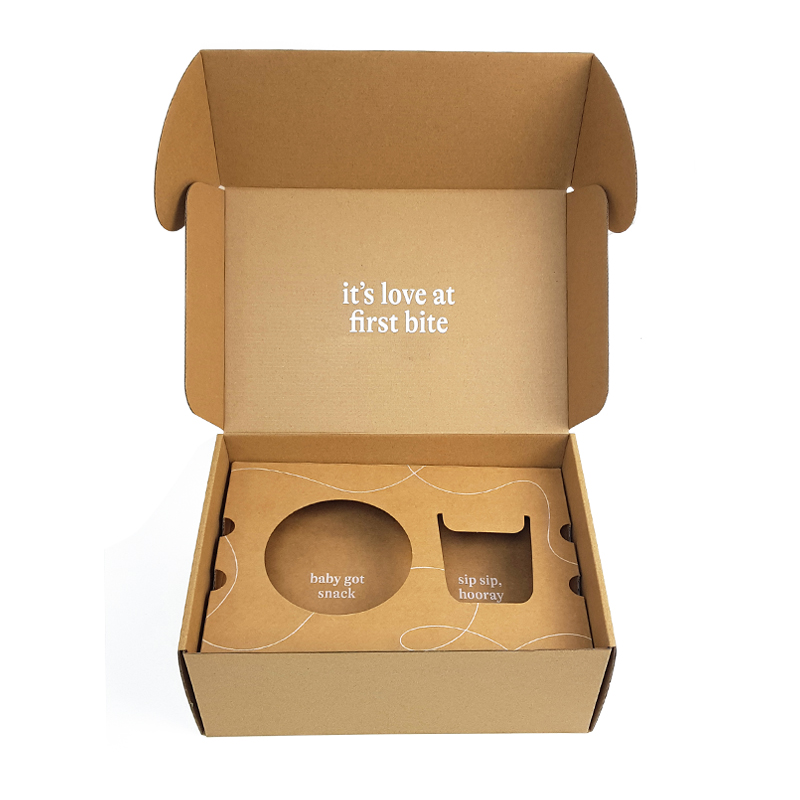
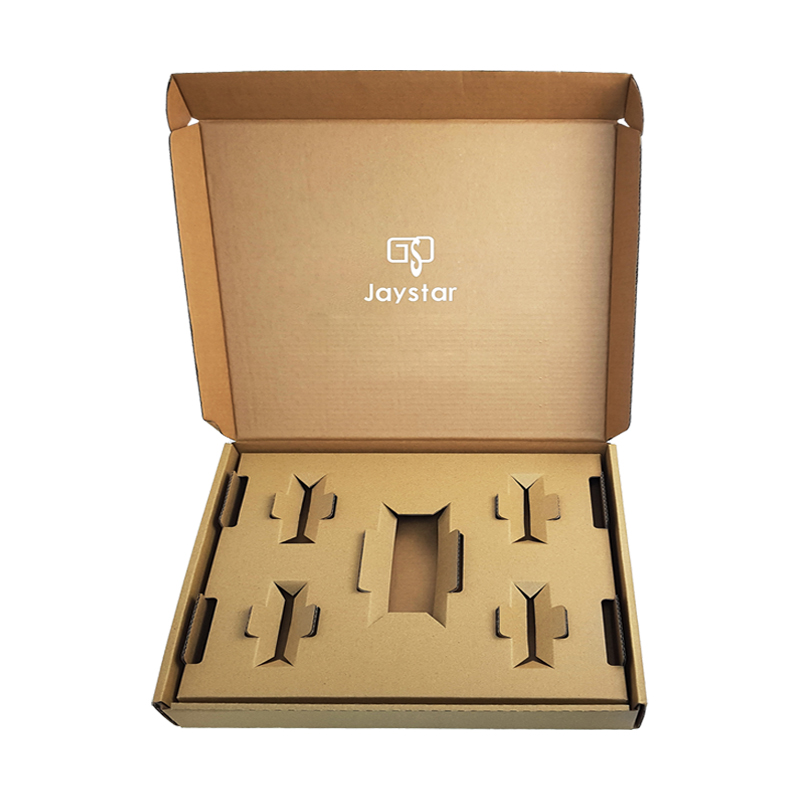
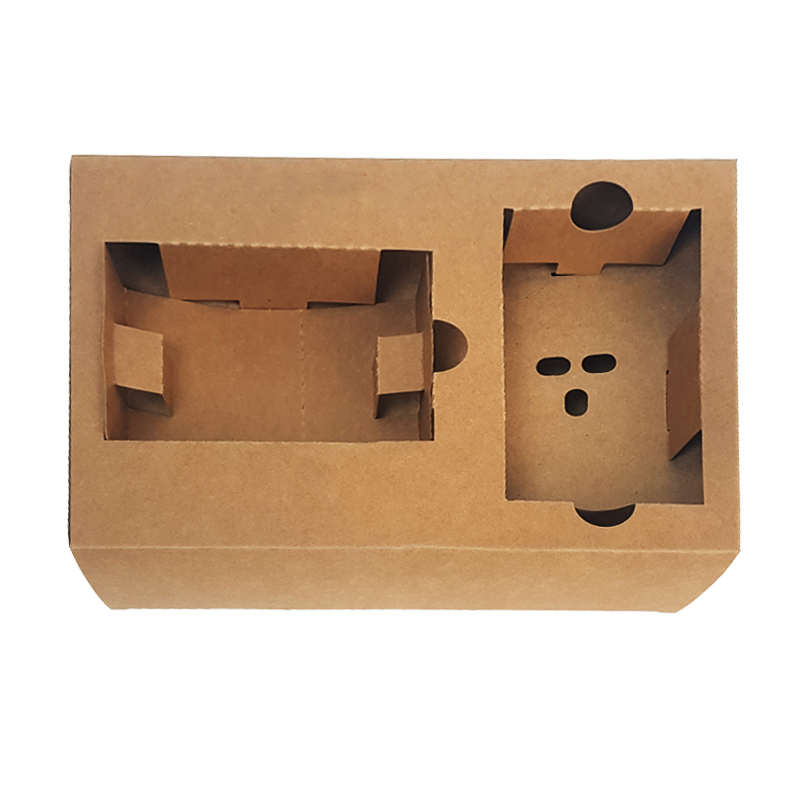
With custom box inserts, there's no 'one size fits all'. The size, weight, and position of products all affect how the insert needs to be structured to secure each product. For reference, here are some examples of common insert structures.
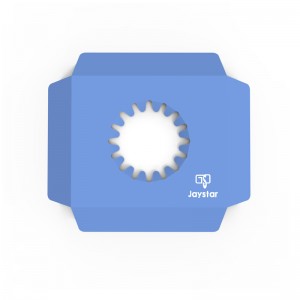
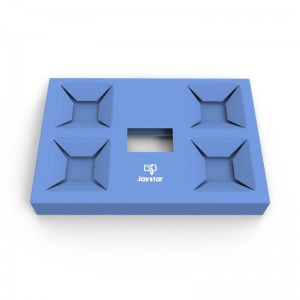
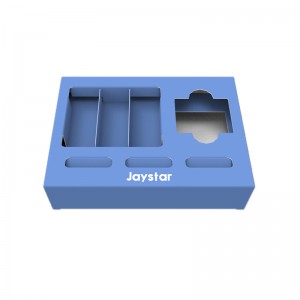
A 7 step process to designing and ordering custom box inserts.

fter passing quality assurance, we'll ship your packaging to your specified location(s).

Add your artwork to the dieline template we'll create for you upon placing your order.

Once your artwork is approved, we'll start production, which typically takes 12-16 days.



Start a structural design project with us to receive an insert and box design that's been tested to fit your products.
Get a sample of your mailer box to test size and quality before starting a bulk order.
Choose your preferred shipping method and place your order on our platform.
All packaging is printed with soy-based ink, which is eco-friendly and produces much brighter and vibrant colors.Box inserts that are corrugated (the wavy lines in cardboard) are stronger and ensure the insert is sturdy. Corrugated inserts are typically used for heavier items, fragile items, or items that will be shipped and need extra cushioning/protection.Ideal for large boxes and heavy items, with a flute thickness of 2.5-3mm.A plastic coated layer that protects your designs from cracks and tears, but not eco-friendly.Most commonly used option and has a flute thickness of 1.2-2mm.For accurate brand colors to be printed and is more expensive than CMYK.An eco-friendly water-based coating but doesn't protect as well as lamination.CMYK is the most popular and cost effective color system used in print.Top off your packaging with a finish option that completes your package.Coating is added to your printed designs to protect it from scratches and scuffs.Solid Bleached Sulfate (SBS) paper that yields high quality print.Shiny and reflective, more prone to fingerprints.Creating the optimal insert design requires more than meets the eye. Products come in various shapes, sizes, and weights, which means using the right materials, creating structures to securely hold each product, and ensuring the insert fits precisely with the outer box.
Most brands don't have a structural design team, which is where we can help! Start a structural design project with us and we'll help you bring your packaging vision to life.
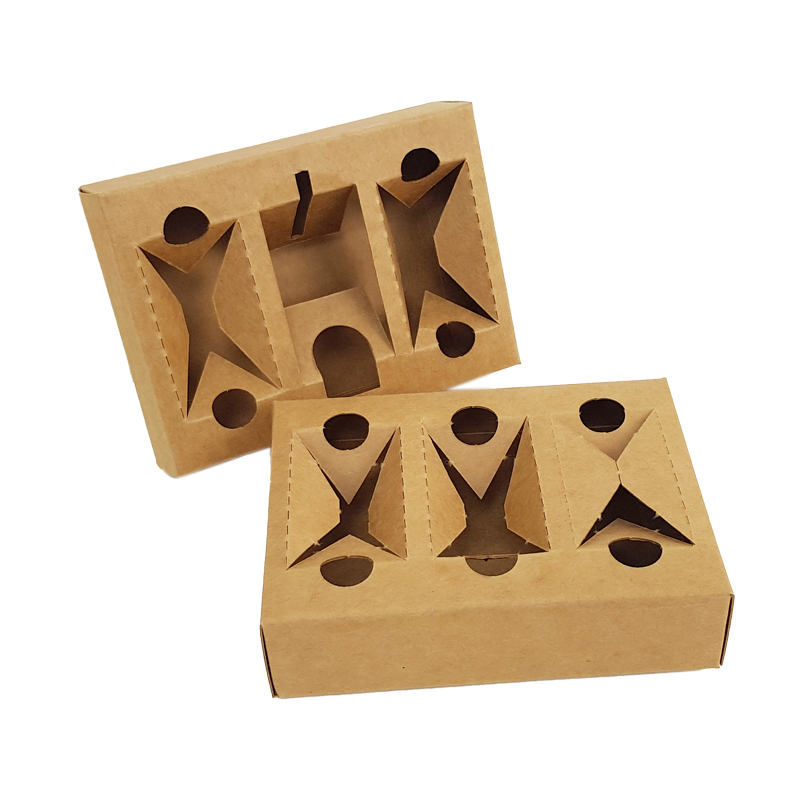
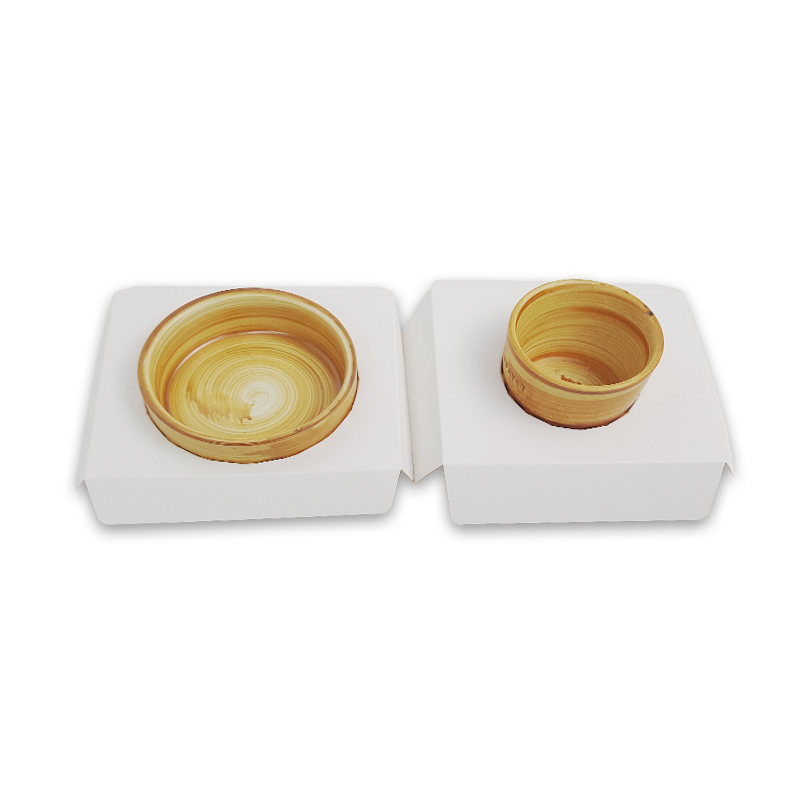
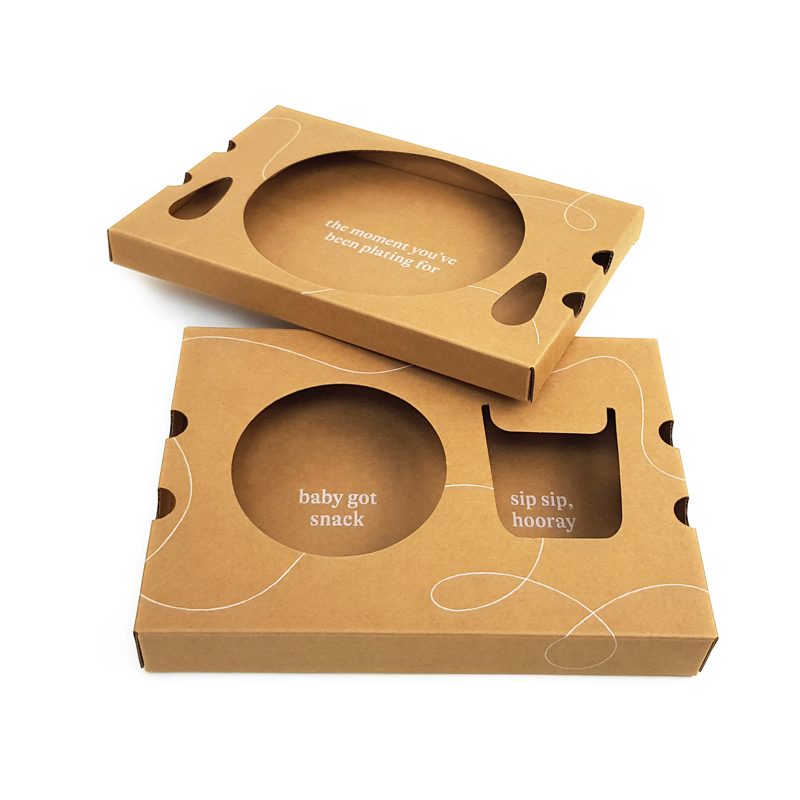
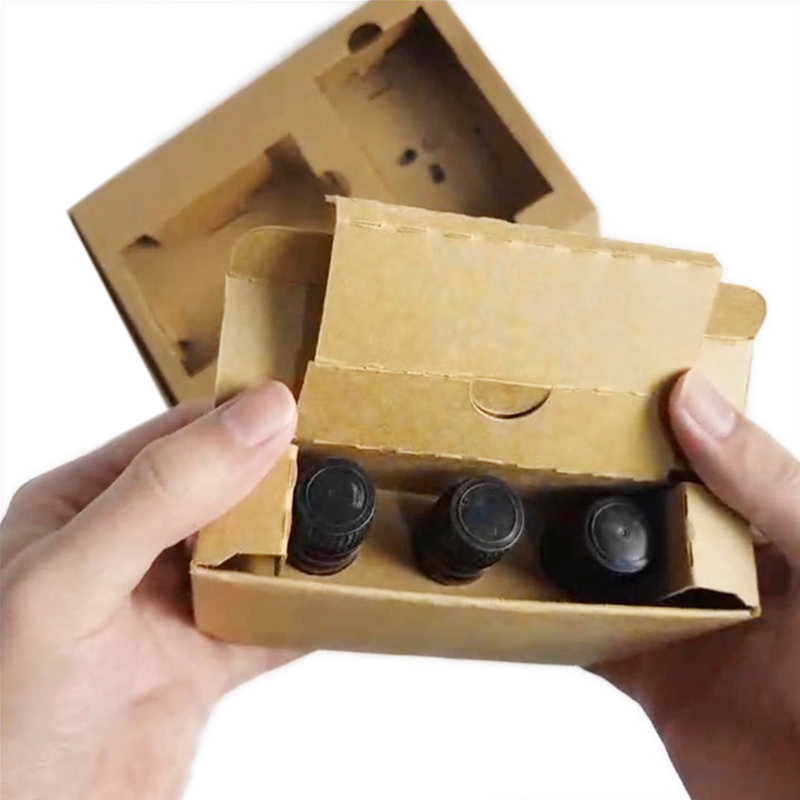

Go to the platform and customize your mailer boxes to get a quote.
Smooth and non-reflective, overall softer look.Designs are printed on these base materials which is then glued to the corrugated board. All materials contain at least 50% post-consumer content (recycled waste).Box inserts that are paper based and not corrugated are typically used for lightweight, non-fragile items. These paper based inserts used a standard thickness of 300-400gsm, and contain at least 50% post-consumer content (recycled waste).We have created a video tutorial on how to assemble double plug and airplane boxes. By watching this video, you will learn the proper assembly techniques for these two types of boxes, ensuring that your products are perfectly packaged and protected.